Grate Firing Systems
We set new standards – with our proprietary grate technology. Our high-performance combustion systems for biomass, municipal waste, and refuse-derived fuels (RDF) enable efficient thermal utilization and sustainable energy generation. From intelligent fuel feeding and precise combustion air systems to reliable ash and slag removal – we provide the complete solution: well-engineered, robust, and from a single source.
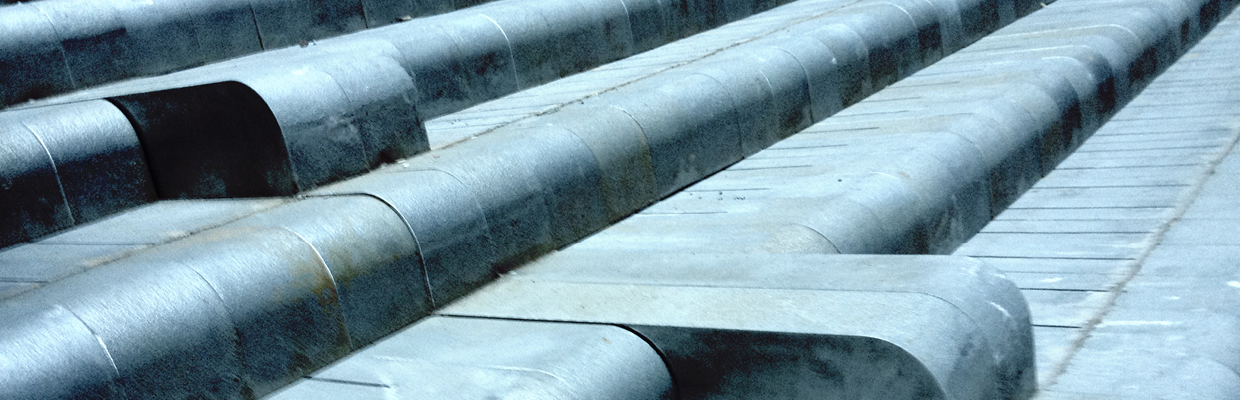
Grate Systems
Whether in power plants for pure steam/power generation or in thermal waste treatment facilities – the combustion systems from Power Service Solutions are used in nearly all areas of energy conversion and are always optimally adapted to the specified requirements.
Environmentally friendly combustion requires special concepts and measures for household and municipal waste, commercial waste, refuse-derived fuels (RDF), residual waste disposal, and all types of biomass. Depending on the heating value of the waste, different grate systems are used. Medium- and high-calorific waste fuels require combustion grates with grate bar cooling systems, such as our self-developed water-cooled moving grate systems. For low- or medium-calorific residues, by contrast, patented air-cooled grate bars are applied.
Moving Grate
The moving grate system from Power Service Solutions is characterized by its robust design and high throughput capacity. External hydraulic drives control the forward feed and return strokes of the movable grate bar rows in each grate zone via a lever system, in accordance with control system requirements. Fixed and movable grate bar rows are arranged alternately along the grate path and are mounted on separate grate frames. The uniform motion sequence and the long forward stroke — made possible by the grate bar design — ensure stable combustion control. Compared to short-stroke systems, this motion sequence results in significantly lower wear. Another advantage is the added cooling effect due to the overlap of the grate bars, achieved through the long stroke reaching up to the head of the grate bars.
Roller Grate
In addition to the moving grate system, a Power Service Solution roller grate system can also be used depending on the application. The robust roller grate system is modular in design, consisting of six grate rollers, and is used for low- or medium-calorific residual materials. A portion of the roller surface area continuously rotates through the combustion chamber, while the side facing away from the combustion zone is air-cooled. This alternating exposure reduces the thermal load on the grate surface.
Grate Bars for Moving Grates
The choice of grate surface depends on the specific energy potential of the fuel. Accordingly, air-cooled grate surfaces are used for low-calorific waste fuels, while water-cooled grate surfaces are used for higher-calorific fuels, as they can withstand greater thermal loads.
The grate system is designed to allow a change between water-cooled and air-cooled grate bars at any time without structural modifications. In the transitional range between low- and high-calorific waste, both cooling methods can be combined. The grate bars in the high-temperature combustion zones are water-cooled, while the grate bars in the burnout zone are purely air-cooled.
The grate surface developed by Power Service Solutions enables a process-optimized reduction of primary air input, along with a decrease in excess air, and thereby also a reduction in NOx formation.
Operational Advantages
- Availability > 8,000 operating hours per year
- Increased operational reliability
- Extended maintenance intervals
- Reduced ongoing maintenance costs
- Longer service life due to reversible and wear-resistant end-face grate bar technology
- Reduced spare parts inventory
Air-Cooled Grate Bars
Our patented air-cooled grate bars are designed for extended service life. This is achieved through a second wear-resistant end face, which is positioned behind the front face and protected from temperature-related corrosion. When the outer front surface experiences thermal wear, the grate bar remains fully functional, thereby extending the overall service life. The grate bar can also be designed as a reversible bar with two usable sides, further increasing durability.
Application range: Unlimited suitability for low- to medium-calorific heating values.
Water-Cooled Grate Bars
Cast grate bars contain embedded water-carrying cooling pipes that ensure leak-tightness – even at elevated temperatures. In addition, the embedded steel pipe guarantees a defined flow pattern, avoiding turbulence-induced dead zones typical of angular channels, which can pose an overheating risk. At the same time, optimal cooling of the entire grate bar surface is achieved.
Application range: Unlimited suitability for medium- to high-calorific heating values.
Ash Removal and Deslagging Systems
Deslagging and ash removal systems of various designs have been part of Power Service Solutions’ production and delivery portfolio for many decades. This applies both to the removal of slag from the grate combustion system and to the ash transport from all other ash collection points within the thermal waste treatment facility.
Scope of Supply
- Ram deslagger
- Wet deslagger apron feeder
- Trough chain conveyor
- Single-strand chain conveyor
- Screw conveyors
- Lump breakers
- Scraper conveyors
- Vibrating feeders
- Rotary valves
- Single and double pendulum dampers
- Gate valves
- Nozzle conveyors
- Belt conveyors.
Advantages
- Robust design
- Efficient power transmission
- Maintenance-friendly design
- Reliable ash discharge
- Cooled and dry ash (15-20% residual moisture)
- Adaptable to downstream equipment
- No water treatment required for overflow water
- High cost-effectiveness
- Low conveying speed
- High availability
- Low water consumption
- High operational reliability
- Long service life of wear parts
- Low operating and maintenance costs
- Particularly suitable for the transport of bulky and large-sized materials
Ram Deslagger for Grate Slag
Robust, efficient and low-maintenance.
The slag remover consists of a solid steel sheet housing with an internal drive shaft and a discharge ram. The drive shaft is powered by externally mounted hydraulic cylinders. High force transmission to the ram is achieved through large external and internal lever arms.
Trough Chain Conveyor for Grate Drop Ash
Reliable under extreme conditions.
The trough chain conveyor is designed as a two-strand chain conveyor. The conveyor chain used is a drop-forged forked chain with carriers. The main trough is horizontal, while the drive and deflection segments are arranged at an incline, so that the drive and deflection shafts with their respective bearings are positioned above the water level.